Disclosure Information
This blog contains affiliate links. If you make a purchase through one of these links, our team may earn a commission at no extra cost to you. Learn more. Thanks for your support!
Effective inventory management has become a critical factor separating successful companies from struggling ones. The right inventory management software doesn’t just track products—it transforms operational efficiency, reduces costs, and drives growth.
According to a recent study by Wasp Barcode Technologies, businesses that implement inventory management software report an average 25% reduction in out-of-stock incidents and a 30% improvement in order fulfillment rates (source: Wasp Barcode State of Small Business Report, 2024).
This comprehensive guide will explore the best inventory management software solutions available in 2025, examining their features, benefits, pricing models, and ideal use cases. Whether you’re a small retail operation or a multinational corporation, you’ll find the insights needed to make an informed decision.
The Quick Overview: Best Inventory Management Software
- Best Overall: NetSuite Inventory Management, Zoho Inventory, Fishbowl Inventory
- Best Cloud-Based: Cin7, TradeGecko, Orderhive
- Best for Small Business: inFlow Inventory, Sortly, Stockpile
- Best for Retail: Lightspeed, Vend, Square
- Best for Manufacturing: MRPeasy, Katana
Understanding Inventory Management Software: More Than Just Counting Stock
What Is Inventory Management Software?
Inventory management software is a specialized solution designed to track, manage, and organize product sales, material purchases, and other production-related information. It serves as the technological backbone for modern supply chain operations.
Unlike basic spreadsheets or paper-based systems, dedicated inventory software provides real-time visibility into stock levels, automates reordering processes, and generates actionable insights through advanced analytics and reporting.
The Evolution of Inventory Management
The journey from manual ledgers to sophisticated inventory systems illustrates how this technology has transformed:
- 1970s-1980s: Early computer-based inventory systems
- 1990s: The rise of Enterprise Resource Planning (ERP) systems
- 2000s: Web-based inventory solutions emerge
- 2010s: Cloud-based systems with mobile accessibility
- 2020s: AI-powered predictive inventory management
Today’s solutions integrate with multiple business systems, creating a seamless flow of information across departments and locations.
Core Functionalities Every System Should Have
While features vary between solutions, certain core capabilities define effective inventory management software:
Functionality | Purpose | Benefit |
Inventory tracking | Monitor stock levels | Prevent shortages |
Order management | Process customer orders | Improve fulfillment rates |
Barcode scanning | Automate data entry | Reduce human error |
Beyond these basics, advanced systems offer forecasting tools, multi-location management, and supplier relationship features that further optimize inventory operations.
Key Benefits of Implementing Inventory Management Software
Operational Improvements
Implementing the right inventory software delivers measurable operational benefits that directly impact your bottom line:
- Reduced carrying costs through optimized stock levels
- Minimized stockouts and lost sales opportunities
- Improved warehouse efficiency and space utilization
- Enhanced inventory accuracy and reduced shrinkage
- Streamlined receiving and putaway processes
Organizations implementing inventory management software report average warehouse efficiency improvements of 25-30% (source: Aberdeen Group Supply Chain Visibility Report, 2023).
Financial Advantages
The financial case for inventory management software is compelling:
- Lower working capital requirements through reduced excess inventory
- Improved cash flow by preventing overstock situations
- Reduced operational costs through process automation
- Better gross margins through reduced waste and spoilage
- Enhanced profitability through data-driven purchasing decisions
Many businesses recoup their software investment within 12-18 months through these financial benefits alone.
Customer Experience Enhancement
Often overlooked, inventory software significantly impacts customer satisfaction:
- Faster order processing and fulfillment
- More accurate delivery estimates
- Reduced order errors and returns
- Better product availability
- Improved order tracking capabilities
In the age of same-day shipping expectations, these customer experience enhancements are increasingly important competitive differentiators.
Types of Inventory Management Software Solutions
Cloud-Based vs. On-Premises Solutions
The deployment model significantly impacts implementation, maintenance, and accessibility:
Cloud-Based Systems:
- Lower upfront costs (subscription model)
- Automatic updates and maintenance
- Accessible from anywhere with internet
- Faster implementation timeframes
- Scalable to business growth
On-Premises Systems:
- Complete control over data and security
- One-time licensing cost (higher initial investment)
- Customizable to specific business requirements
- No dependency on internet connectivity
- Potentially lower total cost over 5+ years
The market has shifted dramatically toward cloud solutions, with approximately 78% of new inventory management system implementations being cloud-based (source: Gartner Supply Chain Technology User Behavior Survey, 2024).
Standalone vs. Integrated Systems
Another important consideration is whether to implement a standalone inventory solution or one integrated within a broader business system:
Standalone Systems:
- Focused specifically on inventory management
- Typically more feature-rich for inventory functions
- Generally easier to implement
- Can often integrate with existing systems
- Usually more affordable for smaller businesses
Integrated Systems:
- Part of larger ERP or business management platforms
- Seamless data flow between business functions
- Single source of truth for all business data
- Reduced data duplication and reconciliation
- Better suited for complex operations
The right choice depends on your existing technology stack and the complexity of your inventory management needs.
Top Inventory Management Software for 2025
1. NetSuite Inventory Management: Best for Enterprise Solutions
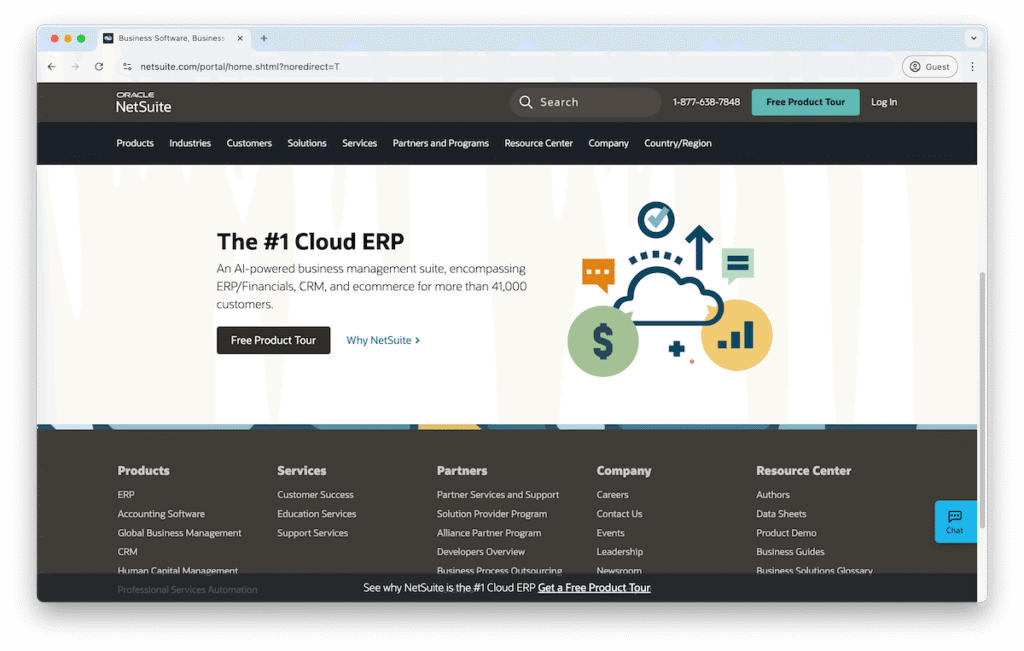
NetSuite offers enterprise-grade inventory management capabilities within its comprehensive cloud ERP platform, making it ideal for scaling businesses with complex inventory needs.
Key Features:
- Real-time inventory visibility across multiple locations
- Automated reordering based on customizable rules
- Advanced demand planning and forecasting
- Lot tracking and serial number management
- Comprehensive warehouse management capabilities
Ideal For: Mid-sized to enterprise businesses requiring robust inventory controls integrated with financials, CRM, and ecommerce.
Pricing: Subscription-based, starting around $999/month plus per-user fees.
2. Zoho Inventory: Best for Small Business
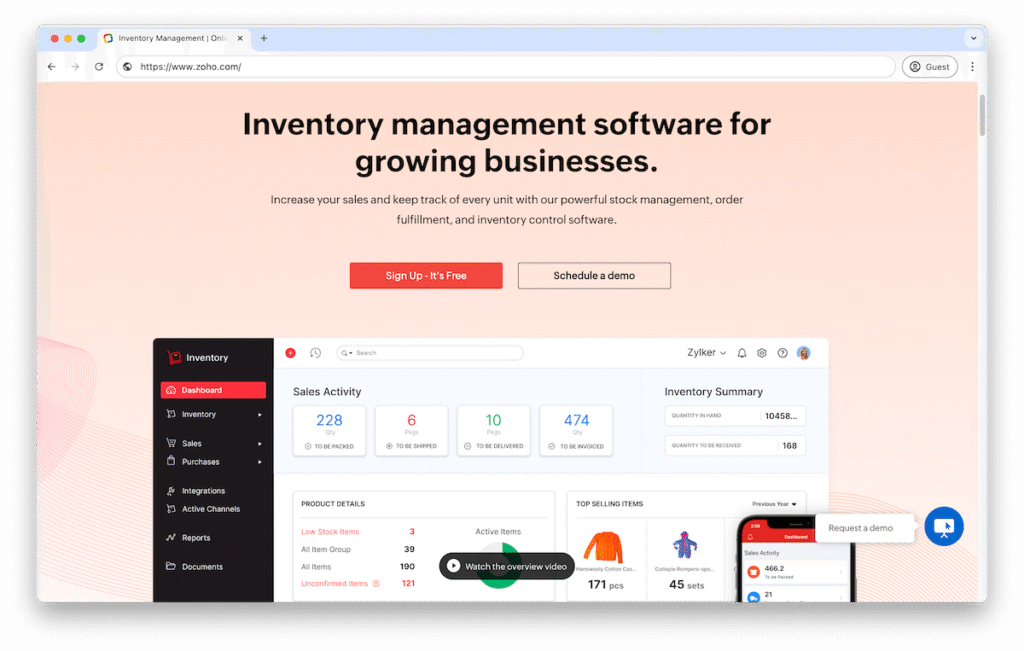
Zoho Inventory delivers powerful inventory management capabilities at an affordable price point, making it an excellent choice for small businesses.
Key Features:
- Order and inventory tracking
- Integration with major ecommerce platforms
- Multi-warehouse management
- Barcode scanning
- Purchase order automation
Ideal For: Small to mid-sized businesses looking for affordable yet capable inventory management.
Pricing: Tiered subscription model starting at $59/month for the Standard plan.
3. Lightspeed Retail: Best for Omnichannel Retail
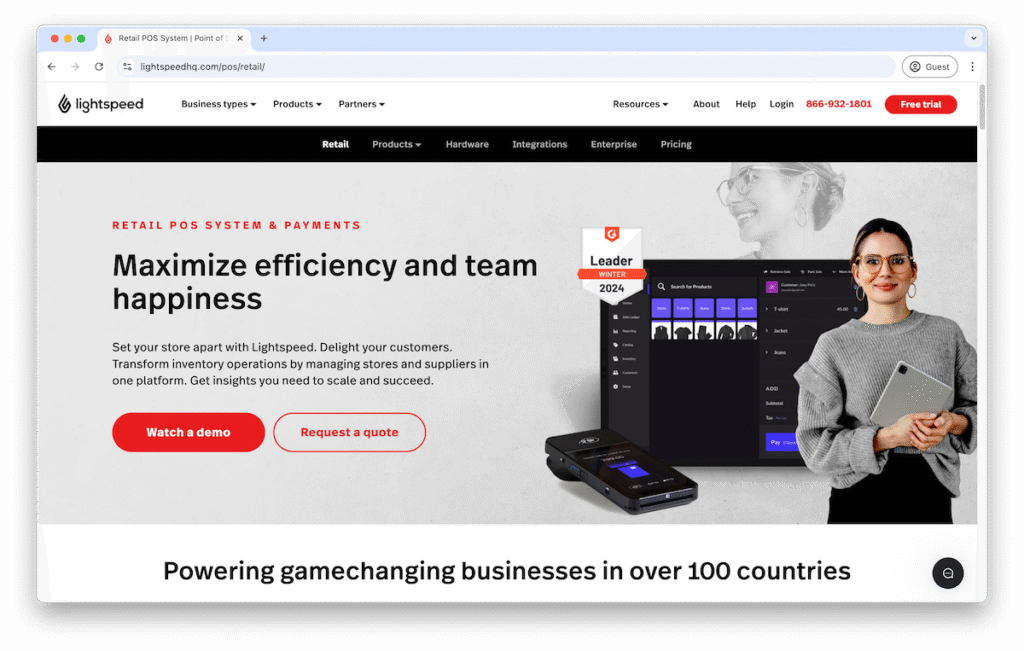
Lightspeed combines powerful inventory management with retail-specific capabilities like POS integration and customer relationship tools.
Key Features:
- Detailed product cataloging and organization
- Bundling and variant management
- Multi-store inventory synchronization
- Purchase order management
- Integrated POS system
Ideal For: Retail businesses with both physical and online stores.
Pricing: Starts at $79/month per location (billed annually).
4. Katana Manufacturing ERP: Best for Production Management
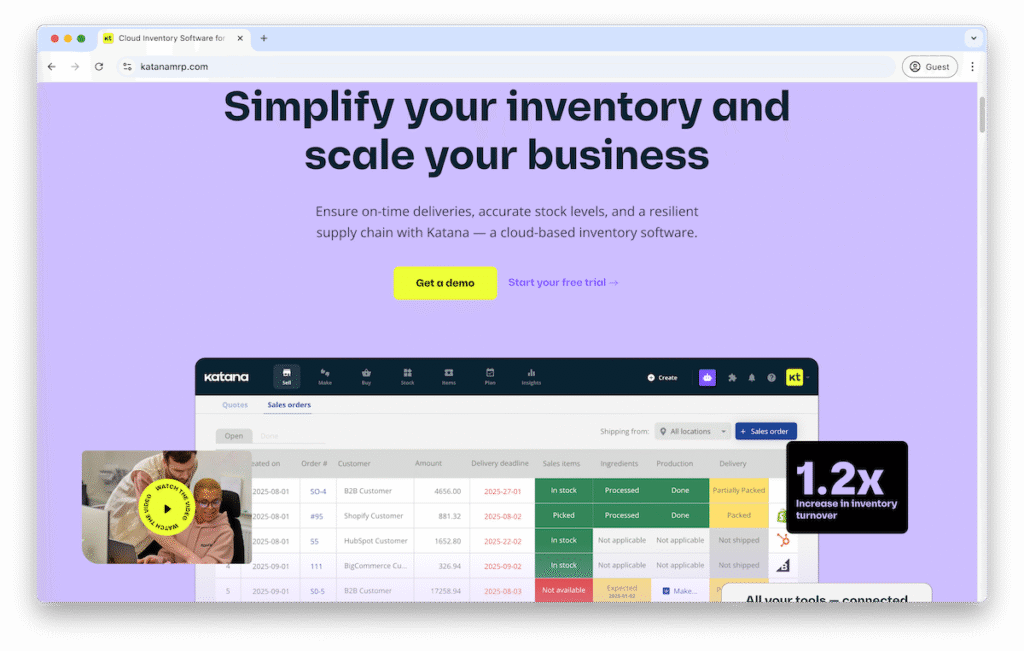
Katana focuses specifically on inventory management for manufacturers, providing tools for raw material tracking, production planning, and finished goods management.
Key Features:
- Real-time manufacturing tracking
- Raw material inventory management
- Bill of materials planning
- Floor-level production controls
- Finished goods inventory tracking
Ideal For: Small to mid-sized manufacturers looking for specialized inventory solutions.
Pricing: Subscription-based starting at $149/month for the Essential plan.
5. Fishbowl Inventory: Best for QuickBooks Integration
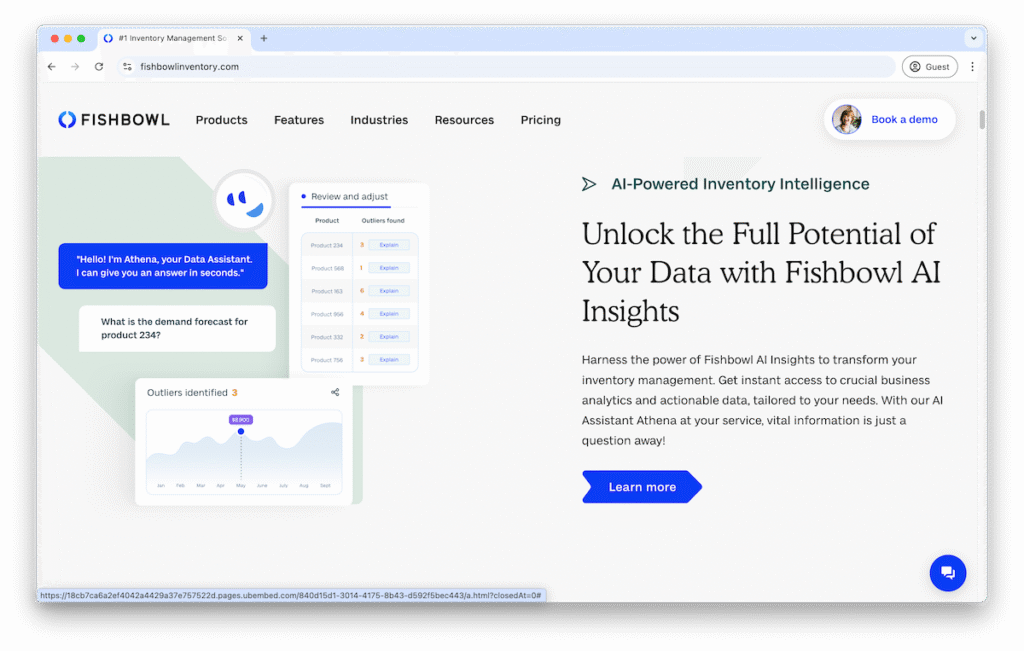
Fishbowl serves the unique needs of wholesale distributors with tools for managing large product catalogs and complex pricing structures.
Key Features:
- Advanced warehouse management
- Multiple location tracking
- Barcode scanning and generation
- Detailed reporting and analytics
- Seamless QuickBooks integration
Ideal For: Wholesale distributors and QuickBooks users needing advanced inventory capabilities.
Pricing: Perpetual license model starting around $4,395 for the first user.
6. Ordoro: Best for Ecommerce Businesses
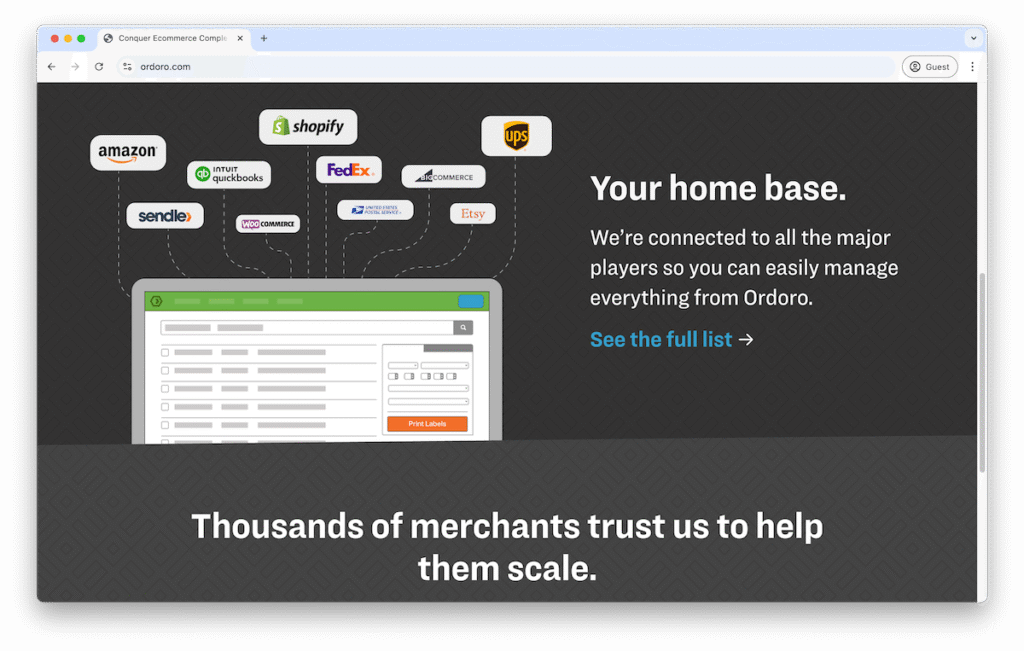
Ordoro specializes in inventory and shipping management for online retailers, with strong multichannel selling capabilities.
Key Features:
- Multi-channel inventory synchronization
- Automated dropshipping workflows
- Batch order processing
- Shipping label generation
- Purchase order management
Ideal For: Ecommerce businesses selling across multiple online marketplaces.
Pricing: Starts at $59/month for the Express plan.
7. inFlow Inventory: Best for Ease of Use
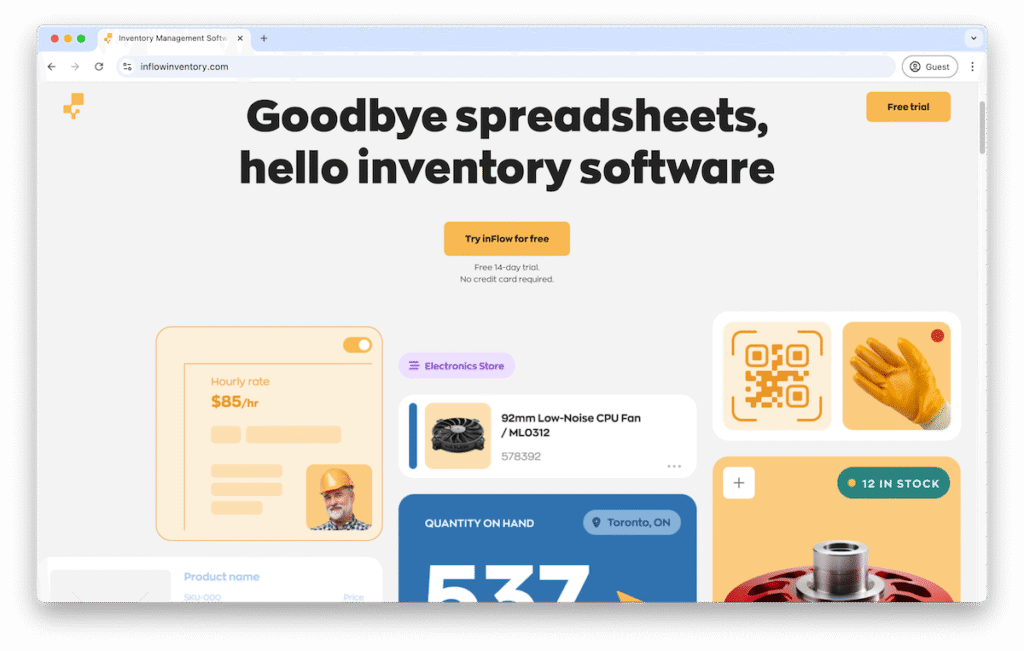
inFlow offers straightforward inventory management with an exceptionally user-friendly interface, ideal for non-technical users.
Key Features:
- Simple visual workflows
- Mobile barcode scanning
- Basic manufacturing capabilities
- Sales and purchase order management
- Customizable reporting
Ideal For: Small businesses seeking simplicity without sacrificing functionality.
Pricing: Starts at $71/month for 2 users (billed annually).
8. Cin7: Best for Growing Businesses
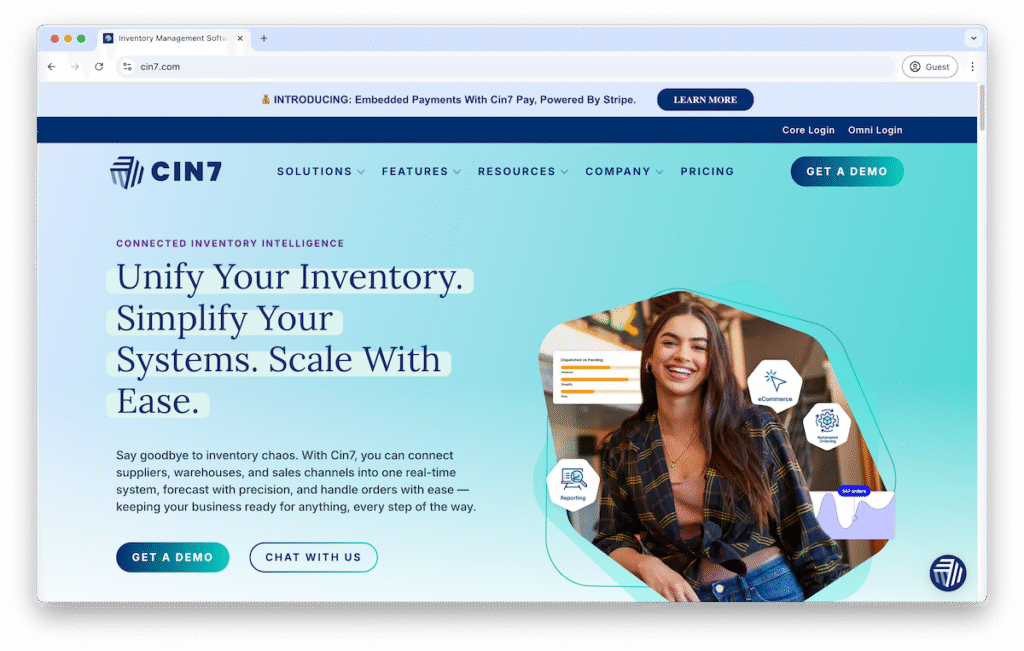
Cin7 provides a scalable inventory platform with built-in EDI, POS, and 3PL integration suited for rapidly expanding operations.
Key Features:
- Built-in B2B ordering portal
- Automated warehouse management
- Branch inventory transfer tools
- Integrated point of sale
- Extensive marketplace integrations
Ideal For: Fast-growing businesses with complex distribution needs.
Pricing: Customized pricing based on business needs, typically starting around $299/month.
Key Features to Look for in Inventory Management Software
Essential Inventory Tracking Features
Real-time inventory visibility sits at the core of effective inventory management. Your chosen solution should track stock across multiple locations and warehouses simultaneously.
Product categorization and flexible attribute management help organize diverse product catalogs. Look for systems supporting different units of measure and automated stock level alerts.
Inventory valuation methods matter for financial accuracy. Strong systems support FIFO, LIFO, and average cost calculations to align with your accounting practices.
The best platforms track not just quantities but also locations, conditions, and other attributes relevant to your specific business needs.
Order Management Capabilities
Seamless order processing integration is crucial for inventory efficiency. Your system should handle sales orders, purchase orders, and backorders within a unified workflow.
Partial shipment capabilities and flexible order prioritization rules are essential for complex fulfillment scenarios. Look for strong RMA processing for managing customer returns efficiently.
The ideal system creates a closed feedback loop between incoming customer orders and actual inventory availability, preventing overselling or stockouts.
Reporting and Analytics
Actionable inventory insights drive smarter business decisions. Your system should provide stock level reports, inventory valuation, and turnover metrics without complex configuration.
Identifying slow-moving inventory helps optimize purchasing decisions. Regular stockout analysis prevents revenue loss from missed sales opportunities.
Demand forecasting analytics transform historical data into predictive insights. Look for customizable dashboards that deliver actionable information rather than overwhelming raw data.
Integration Capabilities
Modern inventory systems must connect with your broader technology ecosystem. Essential integrations include accounting software, ecommerce platforms, and shipping software.
POS system compatibility enables brick-and-mortar retail operations. Manufacturing integrations support production planning based on component availability.
API accessibility and pre-built connectors significantly impact implementation complexity and total cost. Evaluate the integration capabilities based on your existing tech stack.
Implementation Best Practices
Planning Your Implementation
Successful implementation starts with documenting your current inventory processes and pain points. Define clear objectives to measure the success of your new system.
Identify which existing systems require integration with your inventory solution. Create realistic timelines that account for data migration, testing, and staff training.
Most businesses underestimate implementation timeframes. Plan for 3-6 months for complex implementations, depending on your business size and process complexity.
Data Migration Strategies
Clean data is essential for a successful migration. Audit and standardize your inventory data before transferring it to the new system.
Consider a phased migration approach rather than a complete cutover. This allows for thorough validation while maintaining business continuity.
Many implementations fail due to poor data migration. Maintain parallel systems during the transition period and thoroughly document your data mapping process.
Training and Change Management
User adoption makes or breaks your implementation. Identify potential super-users who can champion the system and support their colleagues.
Develop role-specific training that focuses on day-to-day tasks rather than overwhelming comprehensive training. Create easily accessible reference materials for common procedures.
Budget adequately for training and change management. Many organizations spend as much on these elements as on the software itself, with good reason.
Pricing Models and Total Cost Considerations
Common Pricing Structures
Subscription (SaaS) models offer lower upfront costs with predictable monthly or annual payments. These typically include regular updates and ongoing support.
Perpetual licenses require higher initial investment but may prove more economical for stable, long-term deployments. Be aware of annual maintenance fees, usually 15-20% of the license cost.
Tiered pricing structures let you start small and scale up as needed. Evaluate whether user limits or transaction volumes at each tier align with your growth projections.
Hidden Costs to Consider
Implementation services often exceed the software’s price tag. Complex configurations, customizations, and integrations can significantly impact your total investment.
Training costs vary widely based on staff size, technical proficiency, and system complexity. Ongoing support fees ensure you have help when issues arise.
Factor in opportunity costs associated with implementation timelines. A faster implementation with a slightly more expensive solution may deliver quicker ROI through operational improvements.
Cost Category | Examples | Impact |
Implementation | Configuration, customization | Initial setup |
Integration | Third-party connectors | System compatibility |
Training | Staff education | User adoption |
Industry-Specific Inventory Solutions
Retail Inventory Management
Retail inventory demands specialized capabilities like POS integration and seasonal inventory planning. Strong merchandising tools support visual organization and customer-facing stock visibility.
Fashion and apparel retailers need systems handling style/color/size matrices. Omnichannel retailers require solutions that unify in-store and online inventory pools.
Look for retail-specific features like open-to-buy budgeting and integrated loyalty program tracking to maximize sales opportunities.
Manufacturing Inventory Management
Manufacturing inventory systems must handle complex component relationships. Bill of materials (BOM) management and MRP functionality are essential for production environments.
Work-in-process tracking bridges the gap between raw materials and finished goods. Production scheduling integration ensures materials availability aligns with manufacturing timelines.
Quality control and batch tracking features support regulatory compliance and product consistency across production runs.
Food and Beverage Inventory
Perishable inventory creates unique management challenges. Look for robust lot tracking, expiration date management, and automatic FIFO enforcement.
Recipe and portion control features help maintain consistent food costs. Nutritional information tracking supports menu labeling requirements.
Food safety compliance features ensure your inventory practices meet regulatory standards. Temperature monitoring integration supports cold chain management.
Healthcare Inventory Management
Healthcare inventory often involves regulated, high-value items. Expiration tracking and lot number management are non-negotiable for patient safety.
Compliance documentation features support regulatory requirements. Temperature-sensitive tracking ensures medication and supply efficacy.
Look for systems supporting procedure tray management and sterile processing tracking for clinical environments.
Emerging Technologies in Inventory Management
Artificial Intelligence and Machine Learning
AI-powered demand forecasting transforms inventory management from reactive to proactive. Smart algorithms can predict needs based on seasonal patterns, market trends, and historical data.
Anomaly detection capabilities flag unusual inventory movements that might indicate theft, damage, or counting errors. Dynamic safety stock calculations adjust automatically based on supply chain variables.
Supplier performance prediction helps mitigate supply chain risks before they impact operations. These technologies represent the future of inventory optimization.
Internet of Things (IoT) Integration
RFID technology enables real-time tracking without manual scanning. Sensor-based monitoring provides environmental data for sensitive inventory items.
Automated inventory counts using drones or robots reduce labor costs and increase accuracy. Smart shelves detect stock levels continually rather than during periodic counts.
Connected delivery vehicles provide in-transit visibility for better arrival predictions. IoT brings unprecedented real-time awareness to inventory status.
Blockchain for Supply Chain Transparency
Blockchain creates immutable records of inventory movements throughout the supply chain. This technology enables product authenticity verification for high-value or frequently counterfeited items.
Smart contracts automate procurement processes when predefined conditions are met. End-to-end transparency helps identify bottlenecks and inefficiencies.
While still emerging, blockchain addresses longstanding challenges in supply chain visibility and accountability. Early adopters gain competitive advantages in transparency and traceability.
Making the Right Choice: Selection Process
Assessing Your Business Requirements
Start by documenting your specific inventory challenges. Distinguish between must-have features and nice-to-have capabilities to focus your evaluation.
Consider your growth trajectory when selecting a solution. Today’s perfect fit might become tomorrow’s limitation if your business expands rapidly.
Evaluate technical constraints within your organization. Cloud solutions require reliable internet, while on-premises systems need internal IT support.
Evaluating and Comparing Solutions
Create a consistent evaluation framework for comparing vendors. Request demonstrations using your actual inventory scenarios rather than generic presentations.
Speak with reference customers in your industry. Their experiences often reveal strengths and weaknesses not apparent in sales demonstrations.
Assess the vendor’s financial stability and product roadmap. Your inventory system is a long-term partnership that requires a stable, innovative provider.
Implementation Timeline Expectations
Small business implementations with standard configurations typically require 2-4 weeks. Mid-sized businesses with moderate complexity should plan for 1-3 months.
Enterprise-level implementations usually take 3-6 months or more. Complex manufacturing or multi-location rollouts may require 6-12 months for complete deployment.
Factor these realistic timelines into your planning to prevent operational disruptions and set appropriate stakeholder expectations.
Conclusion
Effective inventory management software delivers more than operational efficiency—it transforms your entire business. In today’s competitive landscape, optimized inventory has become essential for survival and growth.
Understanding your specific needs lets you select a solution that turns inventory management from a necessary cost center into a strategic advantage. The right system enhances customer satisfaction, improves cash flow, and drives profitability.
Whether you’re a small retailer outgrowing spreadsheets or an enterprise optimizing complex supply chains, the right inventory management software helps achieve your business objectives more efficiently.
Take time to evaluate your options thoroughly. The perfect solution not only meets your current needs but positions your business for sustained future success.